A probe to clean space.
A biomimetic concept
In order to optimize the operation of the upper stage of a rocket like Ariane 6, we devised a way to recover orbital waste using a swarm of collectively intelligent robots.
it is by observing the bees’ amazing abilities and their pollen collection that inspired us. Both through their individual performance in terms of detection, identification, communication and memory, as well as through their remarkable collaborative efficiency.
While this bee swarm concept, translated into these robots, allows efficient collection that complements the qualities of the upper stage of a rocket like Ariane 6, it opens up many other applications in space.
Whether in security and collaborative support during spacewalks, for logistical assistance or the extension of the life of satellites in orbit or during approaches to asteroids and unknown planets and to discover, their contribution, through their small size and flexibility, will most likely be an advantage alongside probes and humans.
THRIAE: the three nymph sisters of Greek mythology
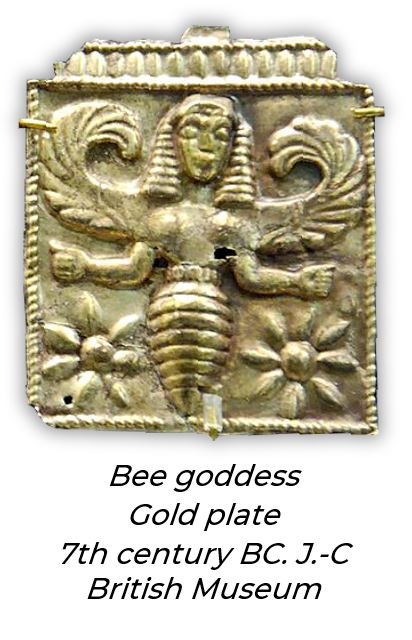
Melaina or Melissa the black, Kleodora said the giver of gifts and Daphnis, also called Corycia the divinations guardian, are the three nymph sisters of Greek mythology. With a woman’s head and a bee’s body, they are associated to Apollo, god of light, harmony, oracle and medicine and Hermes, messenger of Zeus and protector of travelers. Described in Homer’s Hymn to Hermes, these three bee maidens have the power of aiding divination to deliver the truth.
According to a Greek myth, Melissa, after discovering honey, made an offering to the gods, who would then have identified it as divine food.
It was because of the Thriae honey that Apollo grew and developed his adult powers. Thus, Apollo invented a type of divination based on the principle of prophetic stone throwing. The Thriae’s role then was to bring them back to Apollo to revive them.
Reuse an upper stage to collect space waste
The original idea is very simple: the top stage of a rocket is like a large hollow cylindrical volume. From there to imagine that one can fill it with orbital waste to clean up part of the Earth’s orbit, there is only one step.
Throwing away your waste: here is an act of extreme banality and yet saving and complex. Why is it complicated? Because we must already spot the object to be thrown, grasp it with our hand and grasping is a human attribute that not all living beings have. Then you have to take it to a place predefined as going to contain the waste: a trash can. Open then close the cover.
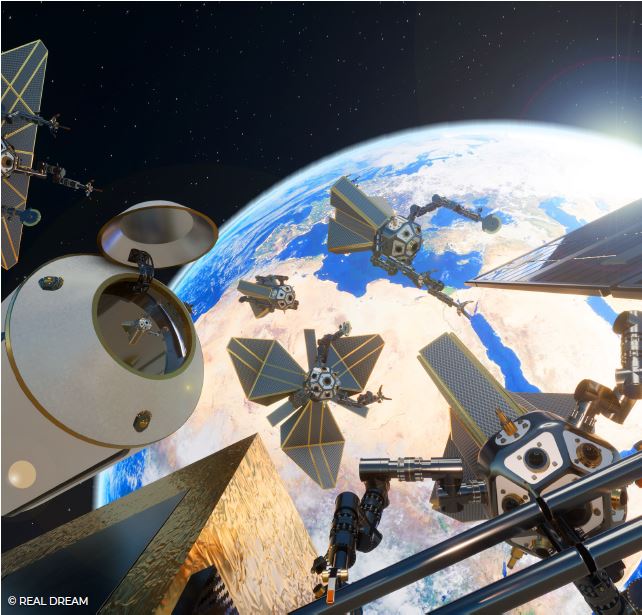
The top stage of a launcher, once its payloads were released, immediately struck us as the ideal container. With its 70m3, the LOX tank can contain a significant amount of space waste. However, in space, we lack « eyes » to locate and especially « hands » to retrieve objects. It is this complex natural limb that we need to recreate.
We thus imagined eight robots to play the role of “space hands”.
They will be small, like CubeSats, and maneuverable with small engines. They will have tools, such as articulated arms, a grinder to cut, everything necessary to grab objects and reduce them, « dismember » them so that their size decreases.
They can act like a fishing net with a wide collar that will be deployed, or even turn into a cage like origami. Finally, they will be coordinated with each other like a swarm of bees in and around a beehive.
Upper stage modified with new functions
Following its satellite placement mission, and according to a previously identified collection scenario, the stage will position itself near the target waste, orient itself in their direction and come to a stop.
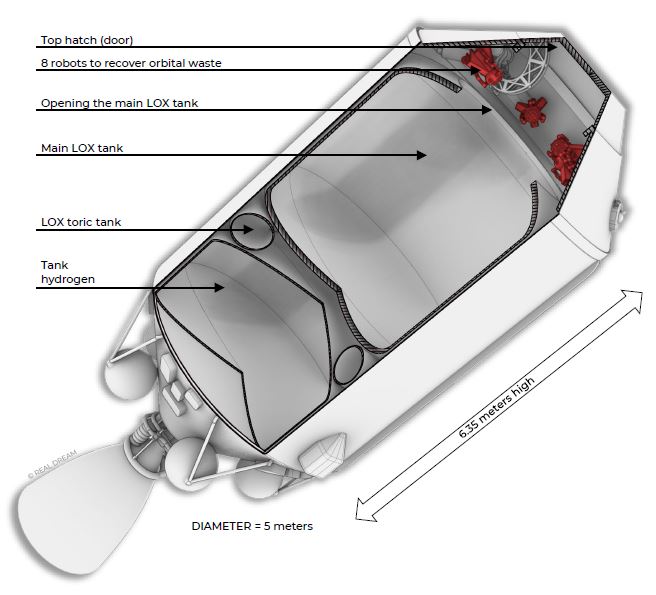
An opening device fitted at the top of the Payload Adapter (ADCU), with a diameter of 2.25m, will allow the exit of the eight robots which will be guided to a starting plane provided for in the mission scenario.
The main LOX tank after emptying and flushing with nitrogen will be cut off on its front base by a pyrotechnic cord.
This front bottom, larger in diameter than the opening of the ADCU, will remain in the LOX reservoir which will then become the receptacle for the orbital waste to be collected.
At the end of the collection, the robots will return to the upper stage, under the part of the ADCU that will be closed and the main engine of the stage will be re-ignited, this time using an additional toroidal tank of LOX to go on a second waste mission, that is to allow the braking and deorbitation of the whole.
We can note the elongation of the stage of the order of 10 cm, due to the addition of the additional toroidal tank of LOX placed between the two initial tanks. This reservoir is necessary to continue the collection and deorbitation mission.
Note also the ADCU modified with a reinforced opening plan and the robots in storage position.
Changes: Payload Adapter (ADCU)
The robots in the rest phase will be housed in the lower part of the ADCU.
The ADCU will also support spotting aid beacons for robots. It will be provided in its upper part with an opening device that will release the robots and bring in the waste before closing.
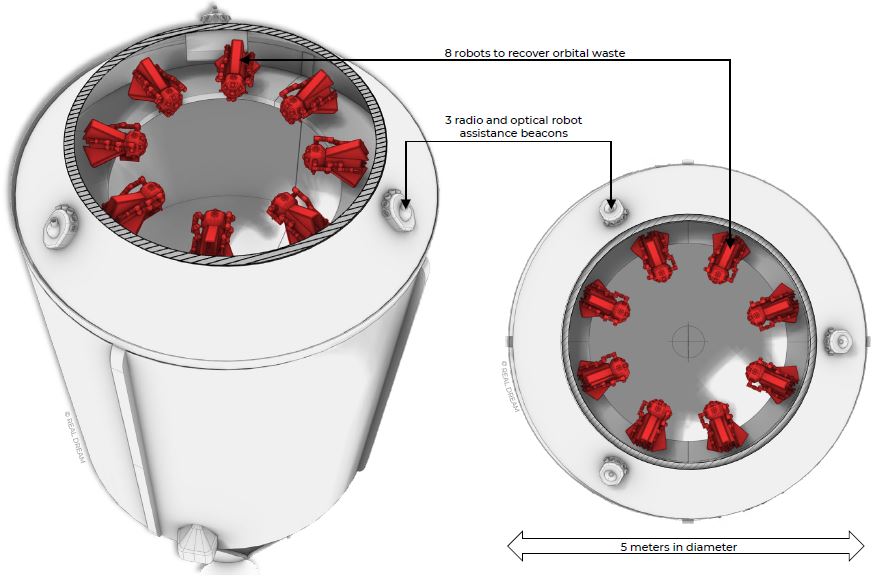
Due to their small size, the ADCU can hold up to eight robots. They are distributed so as to leave room for the opening mechanism and beacons.
There are three radio and optical robot assist beacons for the exit and entry phases (designated by colors: red, green, blue). These beacons delimit a plane perpendicular to the axis of the upper floor and thus facilitate the alignment of the robots on this axis for the exit and return to the ADCU, as well as their grouping on a plane near the waste leaving from collection.
Opening device:
After examining several devices (star panels, iris opening and closing) we chose a motorized door solution because the other devices involved ejecting the upper part of the ADCU which would have generated additional waste.
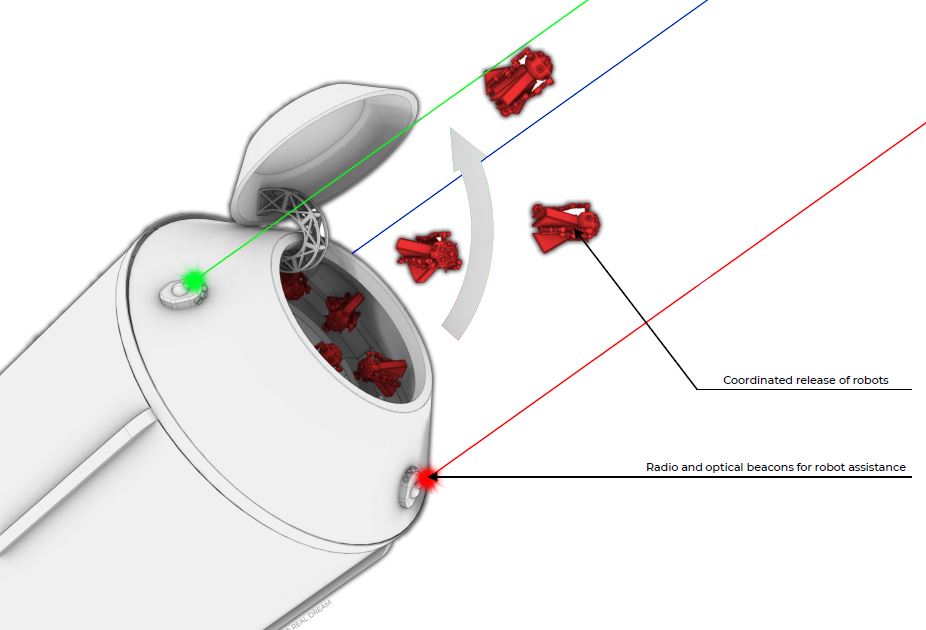
The ADCU is thus separated into two parts, opening a diameter of 2.25m. The lower part is reinforced by a support and centering flange. The upper part (door) is opened thanks to a pyrotechnic bolt sheared in half. Half of them stay on the ADCU, the other half on the door.
An electric motor acts via a worm on a sector which turns an arm integral with the door. The worm gear mechanism used is mechanically irreversible which ensures the positioning of the panel. Reversing the motor direction closes the door and stops it.
Volume filling:
An additional task of the upper floor is to collect « designated » waste beforehand.
This mission will be decided according to criteria of dangerousness in orbit and of the total harvestable quantity, according to the propellants available for the trajectories to be traveled and ultimately deorbitation.
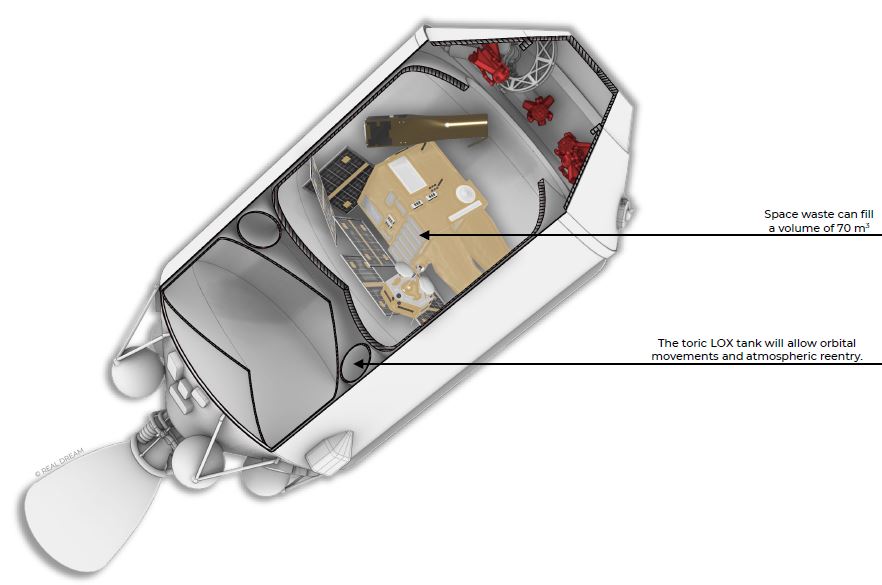
The largest waste is the first to be stored in the LOX tank. The robots then return to their storage position, the ADCU door is closed, and the thruster is turned back on for the remainder of the mission.
The upper floor is positioned near a new waste area, the robot rallying procedure is applied again. Harvesting is done according to the shield formation (explained in § 2.3) the small waste is brought back in order of decreasing size, to allow the highest filling rate.
Return to Nemo point :
Once the orbital trash harvest is complete, the robots return and the ADCU door closed, the upper stage will exit its operational orbit and begin the deorbitation phase.
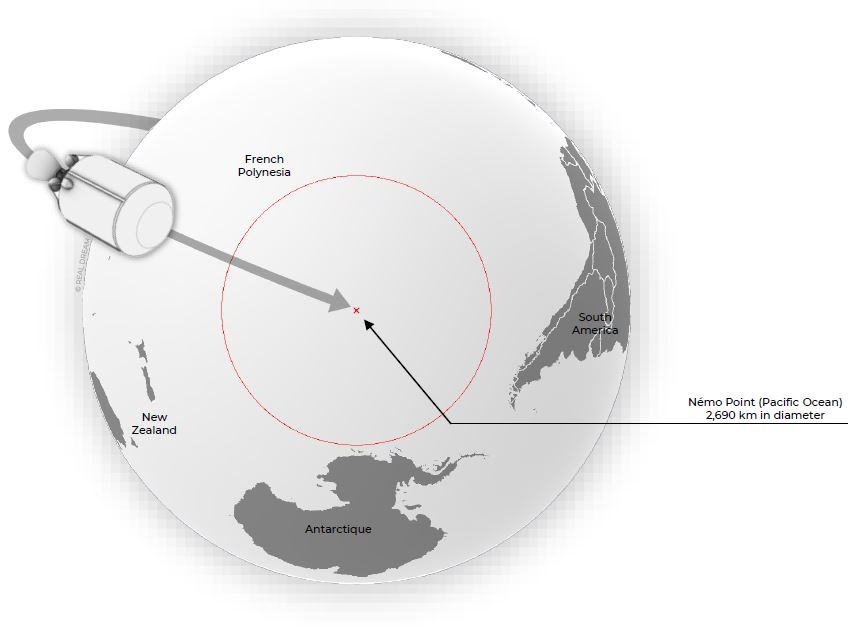
This area, well known for hosting hundreds of space waste, has a security advantage, especially if the hazardous nature of the waste remains active, if not completely destroyed upon re-entry into the atmosphere.
Once the choice of place and time of deorbitation is established and the aviation services have been notified, the stage will initiate, by reversing and braking, a trajectory to target the Nemo point.
Due to the uncertainties about the drop point, it will instead aim, in the axis of its trajectory, at an area upstream of this point, thus leaving as much room as possible for the dispersion of the waste.
A robot inspired by insects: general description
To recover orbital waste, we imagined and designed multifunction robots that can communicate with each other like a swarm of bees.
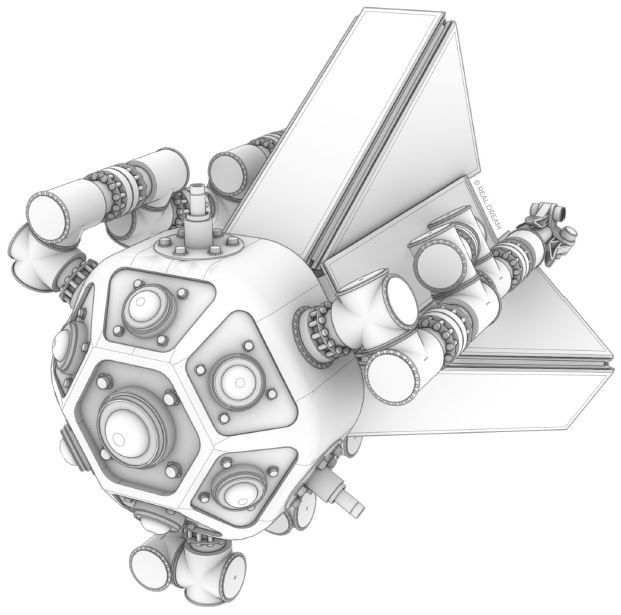
• Robotic arms
Using their three arms, robots can grab floating objects, slice them up, bring them back to the stage, or grab hold of each other to form a train.
• Like a fly’s vision
The front part of the robot can be thought of as a “head”. It is equipped with multiple lenses of cameras, Lidar laser pointers and sensors to allow it to locate itself, to visualize the objects to be recovered over a wide field and to see the general choreography of its articulated arms.
• Deployable wings
Each robot has corolla wings. This device, when deployed, provides an umbrella effect for retrieving items. It is therefore possible either to deflect an object, or to capture and enclose it with the help of two robots, or even to throw a large sail by combining six robots in a hexagon.
• Propulsion and trajectory
A large part of the interior volume is dedicated to the propulsion group. The main plasma or cold gas reactor is located towards the rear of the robot. In addition, on the front (or the « head »), 3 adjustable compressed nitrogen jets allow it to move on the six axes, including backing up to perform all the required maneuvers with precision.
• Other devices
The rear of the wings is made of solar panels to provide a secondary energy. The end of the articulated arms has several tools: drill-driver, grinding wheel, saw …
Side view
Each folded robot has dimensions comparable to those of a domestic oven. It is therefore a small, compact object that can park or navigate in cramped environments.
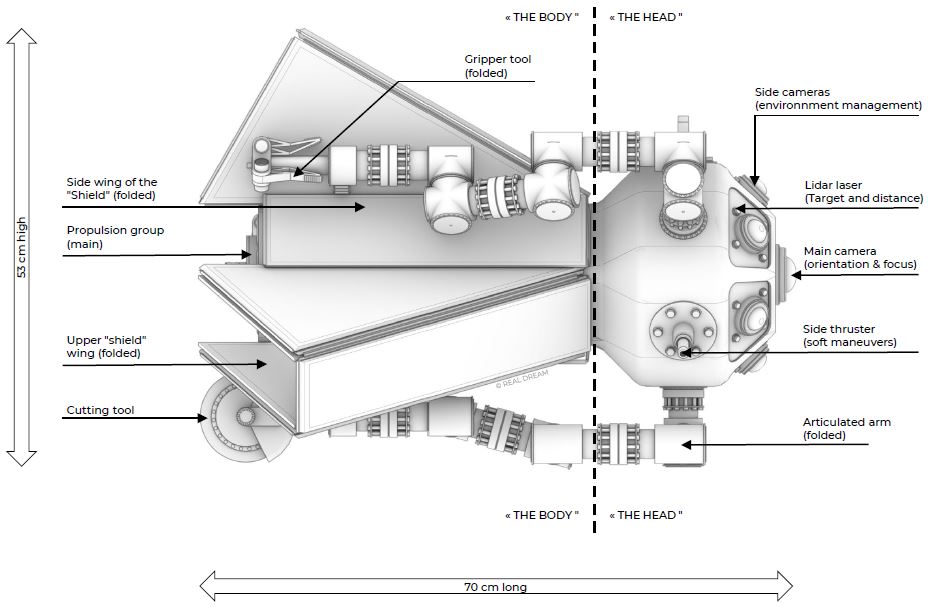
• A « head » at the front
Like the brain of bees, this head has an excellent navigation system, with guidance and piloting calculation functions, as well as an incredible memory of targets (satellites, debris) and approach scenarios. Its « social » structure is extremely elaborate for a coordinated use of robots with distribution / exchange of informations and task.
•The robot’s “body »
The main propulsion power unit is at the rear with batteries and also pressurized compartments (nitrogen, xenon). This is the place where the wings are folded.
Front and back views:
The global layout adopted is an hexagon, it’s shape allows an optimal and collaborative deployment of the « wings ». This is not the only reason: with its six sides, the hexagon fits closer to the circle and allows several elements to be arranged in a minimum of space.
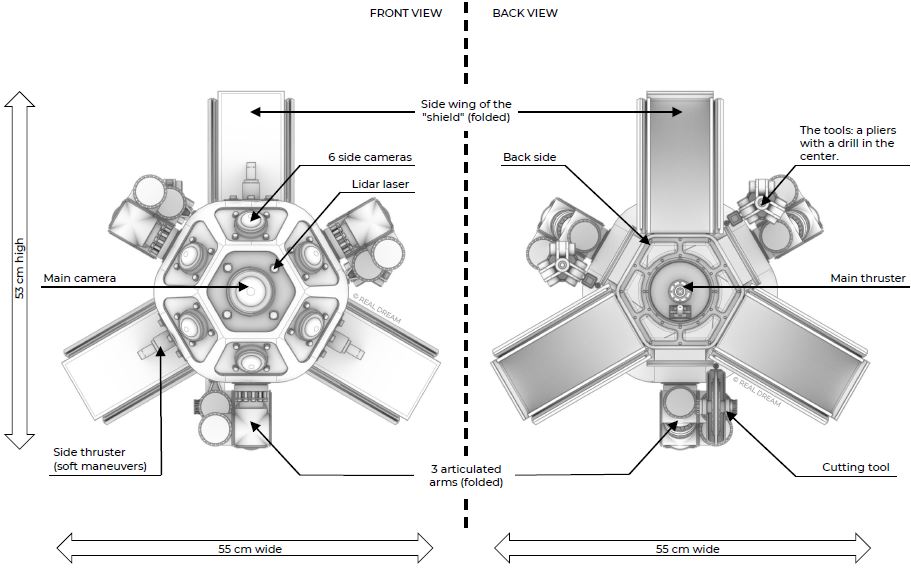
• The front side
The “eyes” of the robot: cameras and Lidar lasers work like those of insects and can process several images simultaneously. The shape of the front and the optics provide a global view over a field of 250°. The sight also extends to the arms and can extend to the rear.
• The back side
The back view shows three folded arms and allows you to see the on-board tools. Two arms have grippers with a drill in the center, the third with a cutting tool. This view also shows the main thruster placed in the center of the robot’s “body”.
In-orbitre covery
The robots coordinate their trajectories and movements to reach a starting position close to the target object. Once this is reached, they will position themselves to hang on to it with their clamps, according to a scenario known in advance and distributed among the robots.
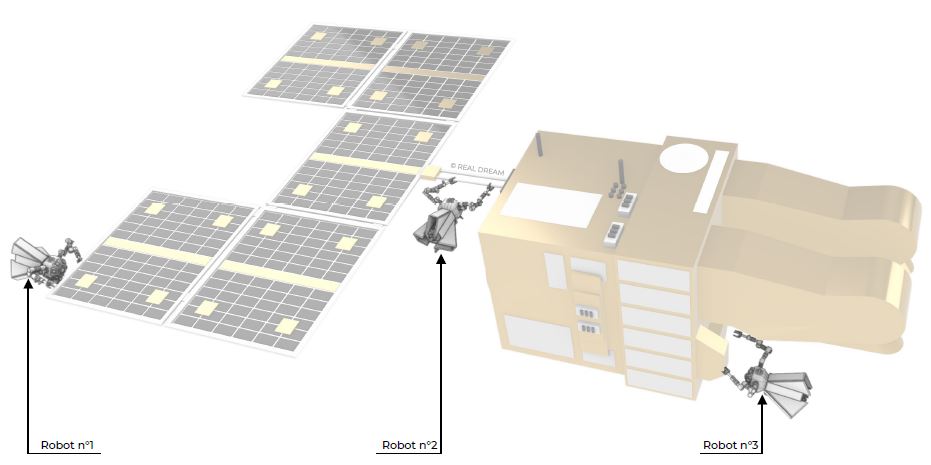
If it is satellites or waste that is too large to enter the upper floor, the robots have the tools to cut them into smaller elements (e.g. photovoltaic panels) and place hooks on sub-assemblies for them. tow.
If it is small diffuse debris, the robots will deploy in groups and unfold their wings to create surfaces, in order to gather the debris, then collect it.
Once they have been collected, the robots will go to the upper floor to deposit the waste in the ex-LOX tank.
In-orbit cutting
In order for the components of a target satellite to take up as little space as possible, they must be reduced so that every piece of waste can pass through the opening – 2.25m in diameter – at the front of the upper floor. In some cases, part of the infrastructure, such as solar panels and antennas, will need to be separated. For this, the robots will use their cutting tools.
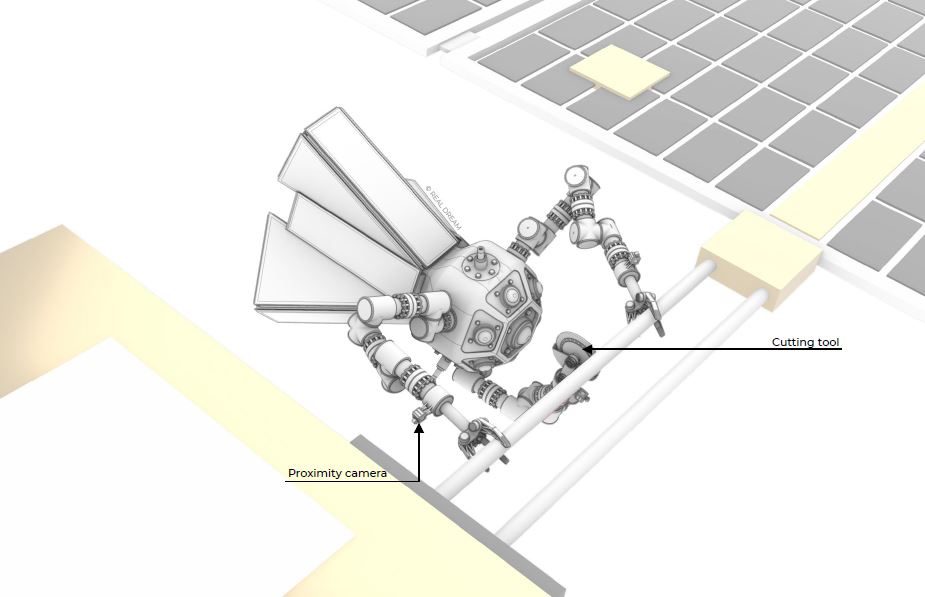
According to a program tested on the ground on a representative model and implanted in the memory of the robots, this intelligent collaboration between the robots will allow:
• Adaptation to various situations;
• The distribution of tools: grinding wheels, pliers, calculators, nibblers;
• The combination of the capabilities of several robots on the same part that is more difficult to process;
• Support by two so-called “back-up” robots for possible failures of others.
Deployment of the « wings » of robots
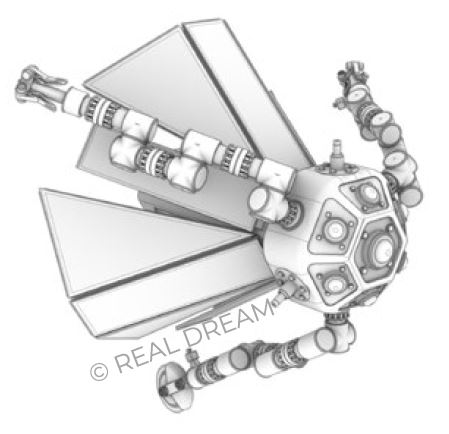
Position 1
• The arms are released forward to let the « wings » open.
•The axis of the « wings » is located just behind the « head » of the robot.
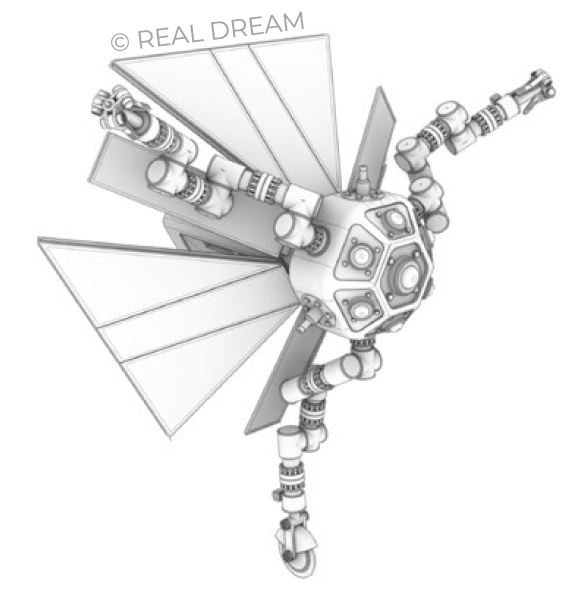
Position 2
• Triangles and rectangular elements of the « wings » are joined so as to form a dish.
•The three rectangles placed on the sides move away from the robot’s body.
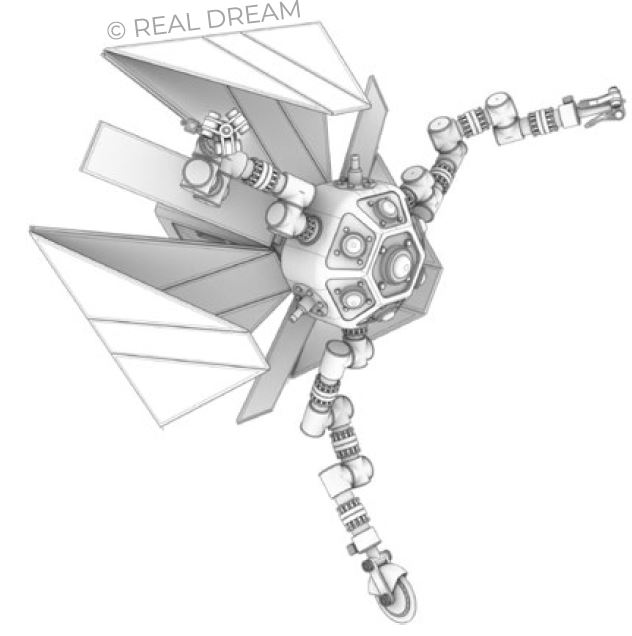
Position 3
• Separation of the joined elements, from this movement the « wings » will take on a larger scale because the surface is multiplied.
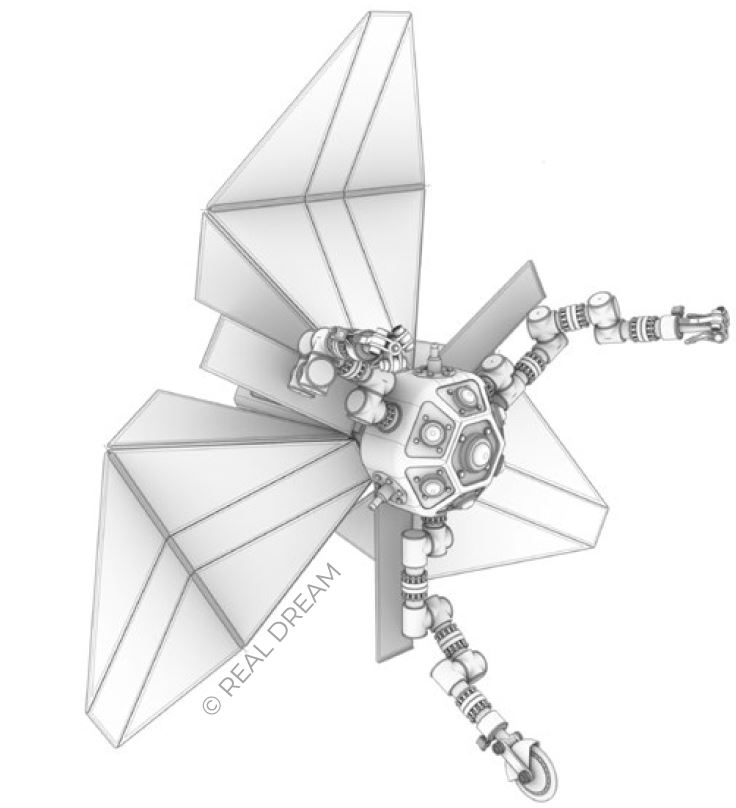
Position 4
• The opening principle is that of a origami, each fold is associated to another for full deployment.
• The three lateral rectangles are in the final position.
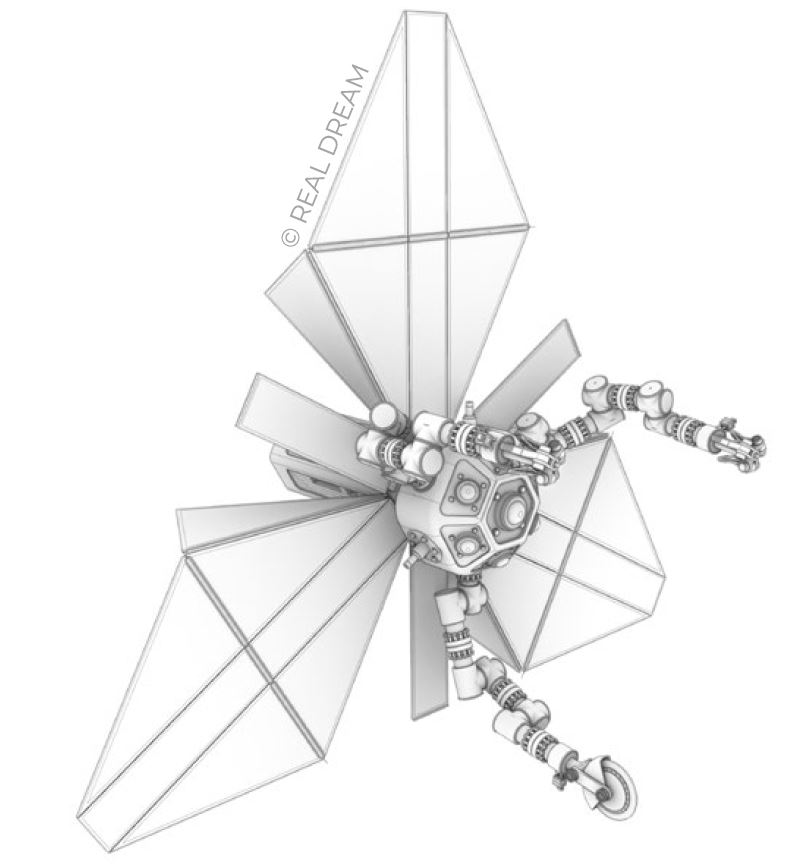
Position 5
• All the pieces are now flat, it only remains to connect the last six triangles to the side members to get the full pattern.
• There are two standard patterns that repeat: a triangle and a rectangle.
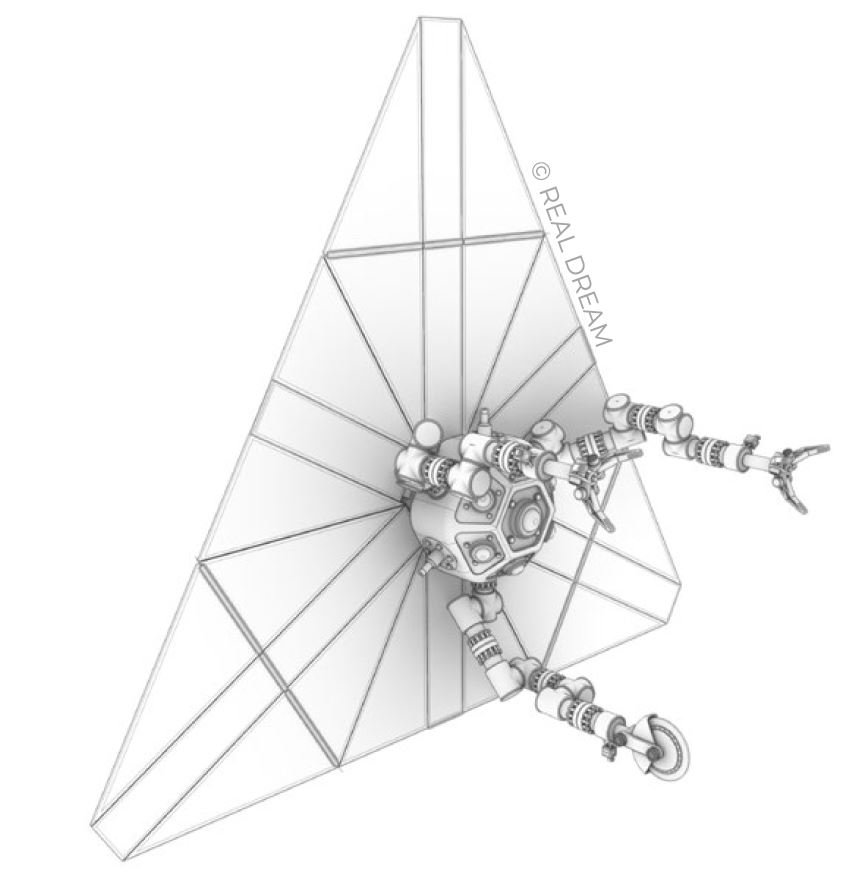
Position 6
•The deployment is complete.
•The total surface of the « shield » is 1,3 m2 based on an equilateral triangle.
Shield training
To go to the collection of small objects, while being sure to recover, it is necessary to create a large area. With its 8 m2, this hexagon represents a broad shield for guiding and positioning an object to ten centimeters without fail.
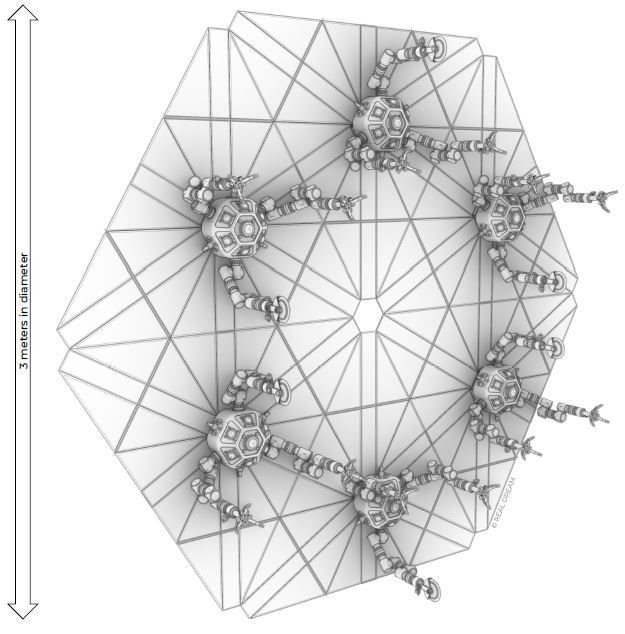
• Guide an object
The goal is to gather in a place as small as possible a number of small waste. For this, the two rescue robots, in collaboration with the shield and the action of his arms, will group the waste to be treated.
• Receive items
With drones simulating robots and representative targets and objectives cases, the scenarios of different maneuvers have been tested on the ground and then transposed in simulation and implemented in the computers robots.
• Capture the piles of debris
In order to be imprisoned by a « cage » of two robots, the groups of waste (or heaps) are first of all « immobilized », that is to say, they have no significant relative movement. relative to the upper stage. The large hexagon can then disassemble, each robot taking a position « start » previously defined around the well formed heap.
• Cage collection
It is exposed in the following plate and requires groups of two robots.
If some waste, although small, are not stable (sheets, cables, rods which may loosen) the collection may be achieved individually by the clamps of robots.
Origami cage
Each robot allows different folding of the wings. In addition to the fold-out positions already seen for the fold-out parking, the capture folds are added.
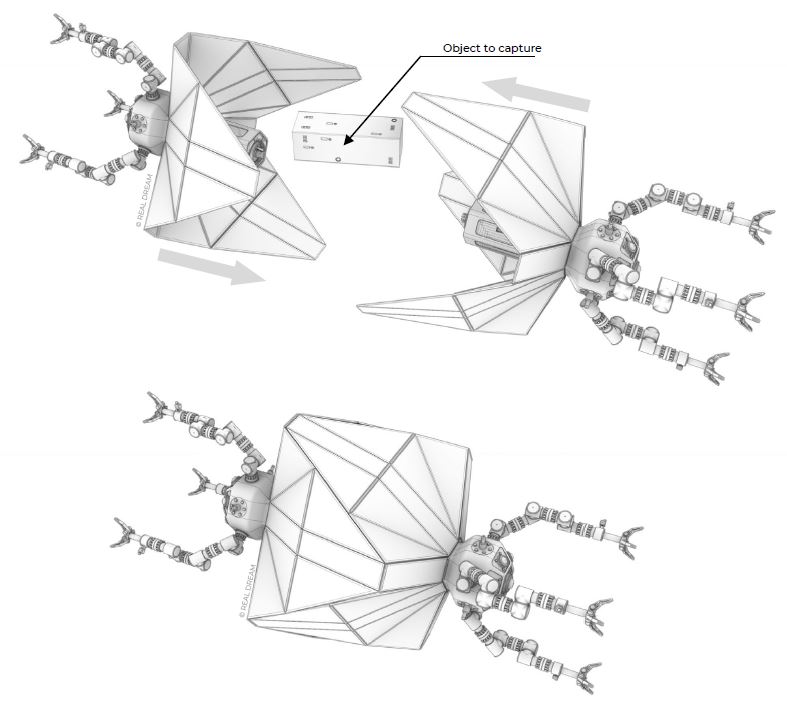
• Unfolding for capture
The origami shape of the wings was calculated to be completely closed in a complementary way by two robots facing each other. The movement of the robots is controlled by the three nozzles placed on each head and oriented accordingly.
•Capture and return
The capture begins with an alignment of the robots on the object to be captured and then a junction. The collaborative « vision » with the rescue robots, perfects the operation. At the end of the operation, a magnetic locking actuated on the rear face of the robots ensures that the closure is maintained.
The return is via a rendezvous path on the axis of the upper stage, followed by the descent guided by the upper stage beacons and robot sensors. With the waste stored in the ex-LOX tank, harvesting can continue.
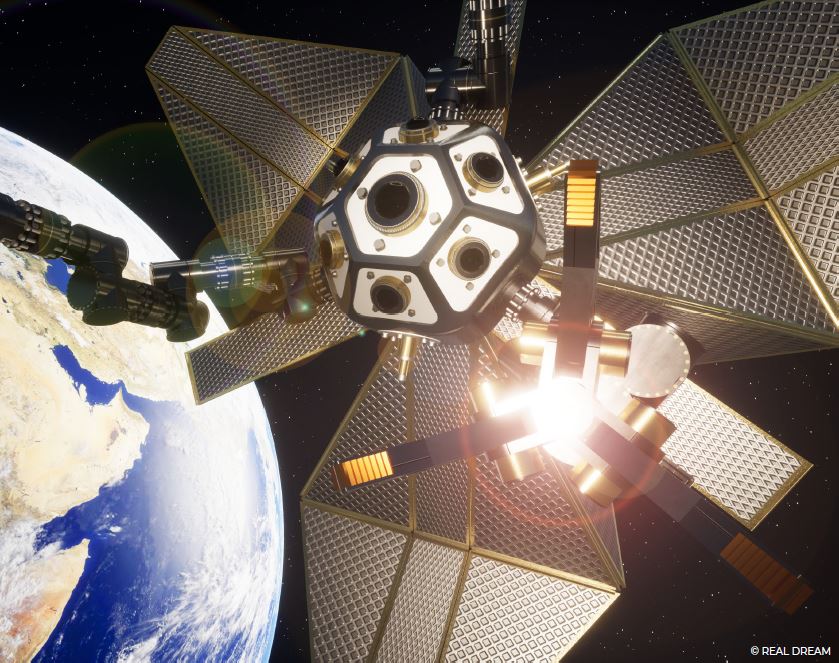
This project and the associated illustrations are the property of REAL DREAM SAS and are protected by the INPI